If you are assembling your own hydraulic hoses in your workshop or for onsite repairs then you may be in need of a hydraulic hose crimping machine that allows you to crimp your own fittings yourself. Not only does this enable you to crimp hoses yourself but it can save time, because you won’t have to travel to the nearest place to have this done by someone else.
Hydraulic hoses are used on all sorts of systems and are made to specific lengths depending on where they are mounted on hydraulic components. By having your own hydraulic hose crimping machine, you no longer have to mount all the components, then measure up the hose lengths and go off to get the hoses crimped only to have to completely re-mount the components again afterwards.
How to operate the hose press machine?
- The first use of hose press machine should be no-load buckling 20 ~ 30 times, observe all parts are normal before use.
- The hose press machine should be used in winter with no-load buckling 20~30 times to make the oil temperature increase some.
- Press the open button to open the mold base and then choose the corresponding mold to install on the mold base according to the specification of the buckled hose and adjust the micrometer scale.
- Place the hose with fittings in the appropriate position in the head so that the full length is buckled at one time.
- Press the buckling button to perform the buckling operation until the head stops buckling and opens the mold automatically.
- Take out the buckled hose assembly and use vernier calipers to check the outer diameter of the buckled joint if it does not match with the parameter table, fine tune the micrometer scale until the next hose buckled meets the requirements.
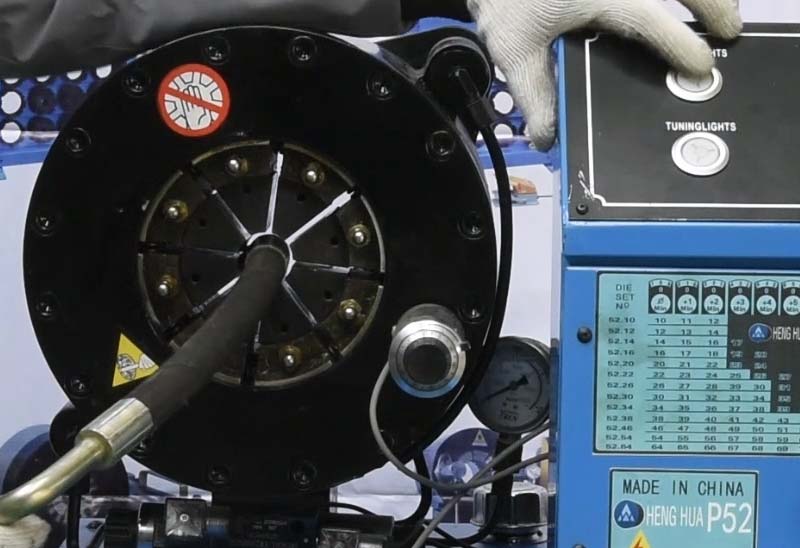
How do you crimp a hose fitting?
Before you crimp any hydraulic hose, you should ensure that you have the correct equipment available.
Recommended safety equipment includes:
- Goggles,
- Ear protectors,
- Strong, protective gloves.
Crimping hydraulic hoses doesn’t need to be difficult. Simply follow the steps below:
- Measure the length of hose your hydraulic system requires and cut to the right length. Before cutting, for critical hose lengths ensure to account for the cut off factor when determining the final length. If the edge of the hose is rough then this should be filed smooth.
- Determine the insertion depth for the hydraulic hose within the appropriate fitting to ensure that once the assembly of the hydraulic system is complete it won’t fail.
- Tip: Mark the insertion depth on the hydraulic hose with chalk to ensure accuracy.
- Choose the correct crimp diameter for each hose, before selecting the correct crimp die set.
- Push the hydraulic hose into the crimping machine and through the crimp die until the hose’s fitting appears above the crimp die. The top of the hose should not be visible above the crimp die.
- Place the compression ring or collar above the crimp die.
- Ensure that you have put on your safety gear.
- Turn on the hydraulic hose crimping machine.
- The crimping machine then pushes the collar that compresses the die and the machine will stop once the collar is at the bottom of the crimp die.
- If you have marked the insertion depth with chalk checking whether the hydraulic hose crimping was successful should be simply. A chalk mark that is no longer at the base of the fitting then this is not a secure crimp and a result of the hose or fitting moving during the crimping process. A chalk mark that has not moved is the sign of a good, secure crimp to a hydraulic hose.
what is the Installation and commissioning of hydraulic press?
What precautions one needs to take While crimping?
- When buckling, place the joint in the center of the die as much as possible and do not press on the hexagonal nut.
- Prevent tools and other foreign objects from entering the head of the hydraulic hose press machine
- Each time after work, the eight die holders must be opened to the maximum extent, so that the spring in the open state to maintain the spring, the cylinder is also in the state of pressure relief to extend the life of the oil seal
- Tank of hydraulic oil more than the hydraulic oil manufacturer specified aging should be replaced, or visual inspection of the oil level table, if the hydraulic oil has been oxidized black must be replaced
- Often to the mold seat moving surface injection of anti-wear lubricant
- Non-pipe press working time, please cover the dust cover to prevent debris fall into the mold seat
Where are the hose pressing machine used?
The hose press machine is also called pipe locking machine, buckling machine, is through the hydraulic transmission of electrical energy through the high pressure oil pump, driven by the hydraulic cylinder into mechanical energy, according to the physics of the area multiplied by the pressure and get more thrust, driven by the contraction and expansion of the pipe press die flap reciprocating movement to achieve the steel jacket firmly fixed on another workpiece machine.
For example, a variety of high-pressure oil hose, pneumatic hose, water hose, concrete hose, automobile cable, steel pipe reduction, etc., widely used in oil fields, coal mines, ship transportation, instrumentation, aerospace, military equipment, construction machinery, agricultural machinery and other industries.
How do you maintenance the press machine?
- Inject anti-wear lubricant into the moving surface of die base frequently
- 2non-pipe press working time, please cover the dust cover to prevent debris into the mold seat
- tank of hydraulic oil more than the hydraulic oil manufacturers specified aging should be replaced, or visual inspection of the oil level table, if the hydraulic oil has been oxidized black must be replaced.
- The Buckling machine maintenance on this simple three steps, the main thing is to pay attention to the staff, in order to do a better job of maintenance of the hydraulic hose pipe pressing machine.
How to distinguish the advantages and disadvantages of the hose pipe press machine?
1 See: is through visual observation of the buckling machine, hose pipe press machine selection of hydraulic parts and electrical components are brand-name products or regular manufacturers of circuit configuration is regular; oil station piping design is reasonable; connection there is no oil seepage; such as the above through visual inspection, you can take the next step of detection.
2 listen: the equipment is connected to the power supply and start, listen to the equipment running sound is normal. If there is abnormal noise, often because the motor and oil pump installation coaxiality is not up to standard, another may be due to the oil pump displacement and pipe diameter selection is not reasonable, and then there is due to the choice of motor or oil pump quality is not very good caused.
3 Measurement: Finally, the main parameters of the equipment are measured
3.1 Let the equipment in the empty running state, touch each mold base block by hand, the hand should not shake phenomenon, otherwise it is regarded as unqualified products.
3.2 Put the equipment on the mold, buckle a sample joint, use caliper or micrometer to measure the buckle joint, roundness and taper should be buckled within 0.1mm is considered excellent.